Go Green.
Go ECO-Built by Eagle
Eco-Built is how we at Eagle describe our efforts to
manufacture our products in an environmentally conscious
way, the same way our customers are focusing their attention
on their environmental impact. It’s an ongoing commitment to
incremental improvements in our manufacturing processes
and facilities to conserve materials and energy while reducing emissions.
Eco-Built is also a process. It’s how we at Eagle set goals for significant reductions in energy consumption, materials usage, and emissions, then create plans to meet those goals. Along the way, we continually monitor progress and continue to push the ball forward.
Eco-Built doesn’t hinder product development or force compromises. To the contrary, ECO-Built helps us make our products better.
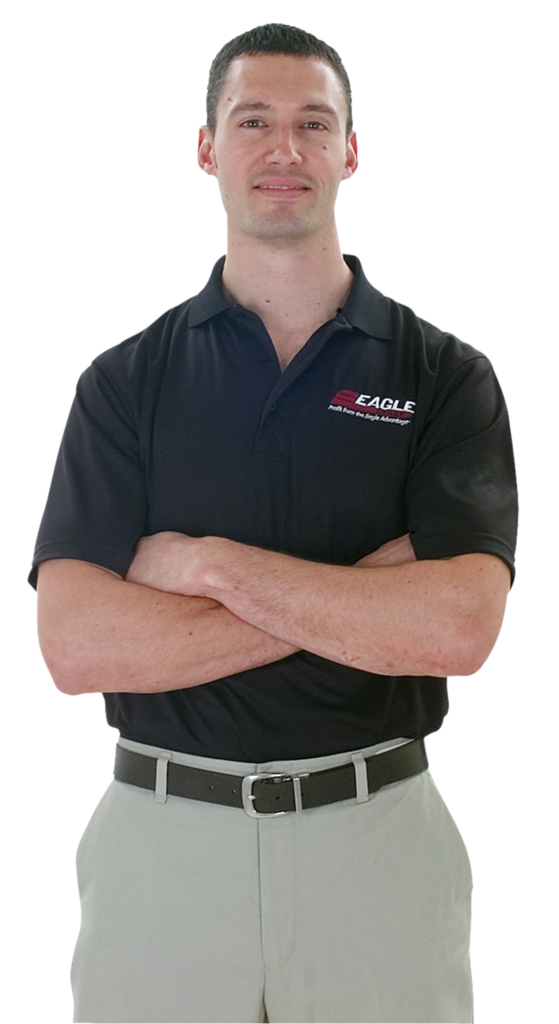
We have to produce products better. It’s a job that never ends.”
Tom Waters
ECO-Built Advocate for The Eagle Group
Numbers don’t lie. Eagle’s efforts to consume less, emit less and conserve more are beginning to bear fruit. Here’s just some of what we’ve been able to accomplish each year.
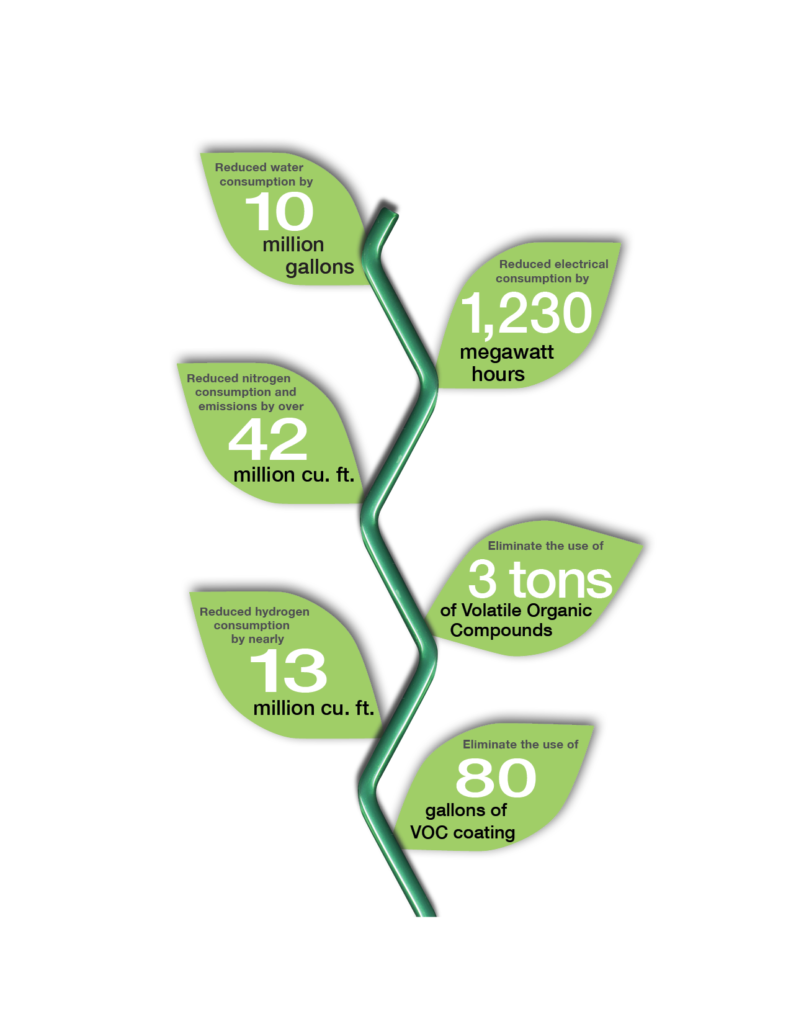
Here’s our commitment to make it happen.
Consume Less.
By consuming less energy and less material, we squander less of the world’s non-renewable resources. That’s why everywhere we look, Eagle is striving to use less to achieve greater results. Less oil, less electricity, less water, less steel—you won’t see the difference in a worktable, wire rack or warming oven, but eventually we’ll all see the difference in the environment.
Emit Less.
By emitting less in the way of chemical solvents and gases, Eagle leaves less of a footprint on our environment. We’ve been able to cut emissions of gases such as hydrogen and nitrogen by many millions of cubic feet, while reducing emissions of VOC (solvents) such as trichloroethylene. The result? Cleaner air and less strain on recycling and disposal systems for noxious solvents.
Conserve more.
By conserving and re-using materials, we put less pressure on non-renewable resources. Not only is Eagle the industry’s largest user of recycled stainless steel, but by installing computer-guided laser cutting machinery, we now use over 85% of the sheet metal that comes into the plant (and recycle the rest of course). We also utilize more recycled energy than anyone else in the industry—20,000 square feet of Eagle’s facility is heated with oil gained from the leftovers of other processes.
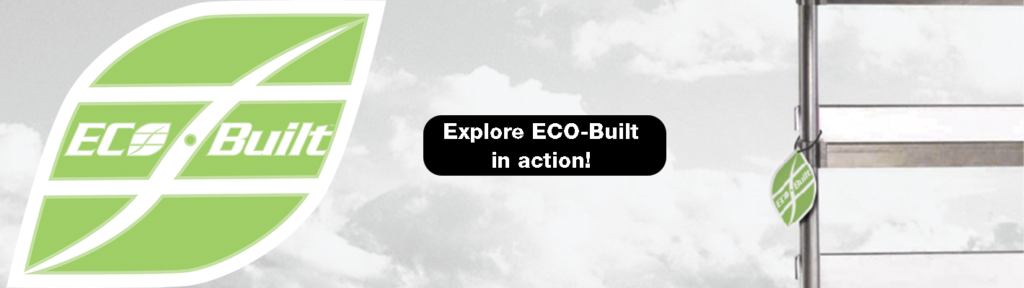